What Are the Advantages of Using Perforated Display Boxes?
Holidaypac
2024-08-30
21345
What Are Perforated Display Boxes
Perforated display boxes are a type of packaging that incorporates perforated lines or patterns, allowing for easy separation of sections or dispensing of products. These boxes are designed to showcase and dispense items in a convenient and visually appealing manner, making them ideal for retail environments. Here are some key features and benefits of perforated display boxes:
Key Features of Perforated Display Boxes
- Perforated Lines: The boxes feature strategically placed perforations that enable customers to easily tear off sections or individual items without damaging the rest of the package.
- Customizable Designs: Perforated display boxes can be customized with various patterns, shapes, and sizes to suit different product types and display requirements.
- Sturdy Construction: These boxes are typically made from durable materials like corrugated cardboard or paperboard to ensure the structural integrity of the package and the products inside.
- Branding Opportunities: The boxes provide ample space for branding, allowing companies to showcase their logos, product information, and marketing messages to attract customers.
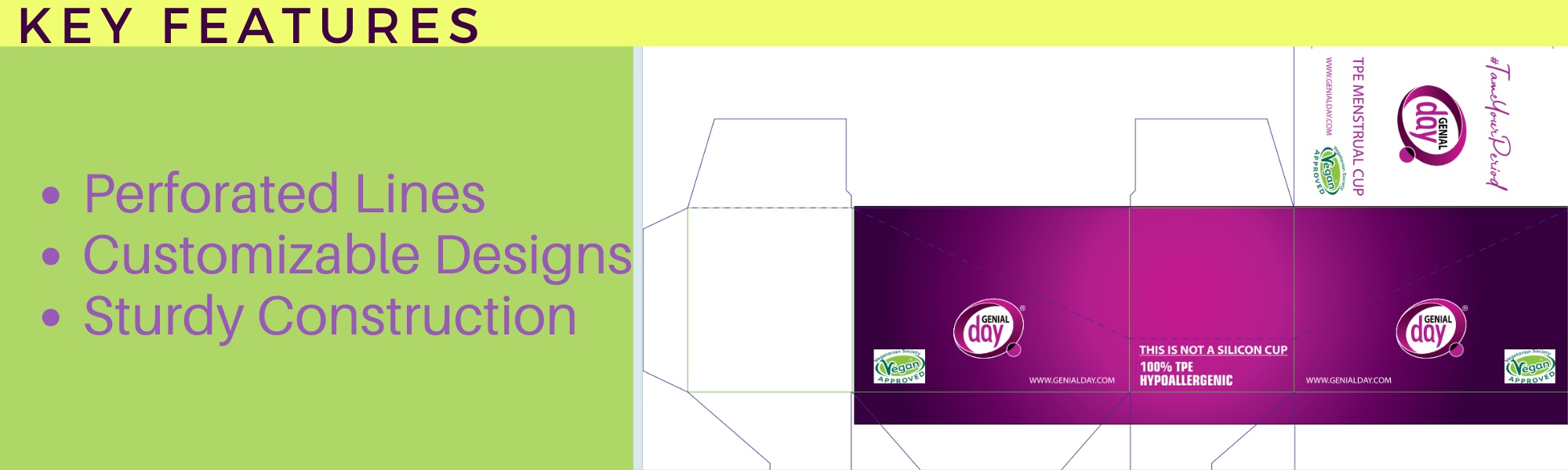
Benefits of Perforated Display Boxes
- Improved Accessibility: The perforated design makes it easier for customers to access and dispense products, enhancing their overall shopping experience.
- Reduced Waste: By allowing customers to take only the items they need, perforated display boxes help minimize product waste and reduce the environmental impact of packaging.
- Enhanced Visibility: The boxes are designed to showcase products prominently, making them more visible and appealing to customers in retail settings.
- Efficient Restocking: When a section is emptied, the box can be easily refilled, saving time and labor for store staff.
- Cost-Effectiveness: Perforated display boxes are often more cost-effective than individual packaging for small items, as they require less material and labor to produce.
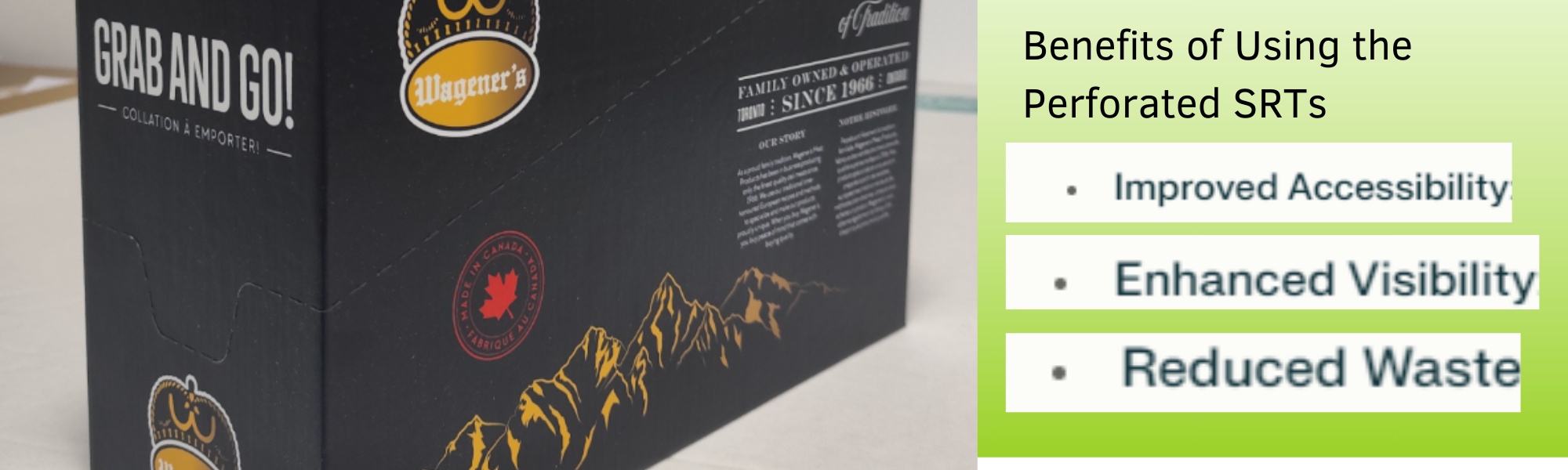
Applications of Perforated Display Boxes
Perforated display boxes are commonly used for packaging and dispensing a variety of products, including:
- Small Retail Items: Accessories, batteries, office supplies, and other small consumer goods.
- Snack Foods: Individual servings of chips, candies, and other snacks.
- Cosmetics: Samples, travel-sized products, and single-use items.
- Hardware: Screws, nails, washers, and other small hardware components.
In summary, perforated display boxes offer a practical and visually appealing solution for packaging and dispensing products in retail environments, providing benefits for both customers and businesses.
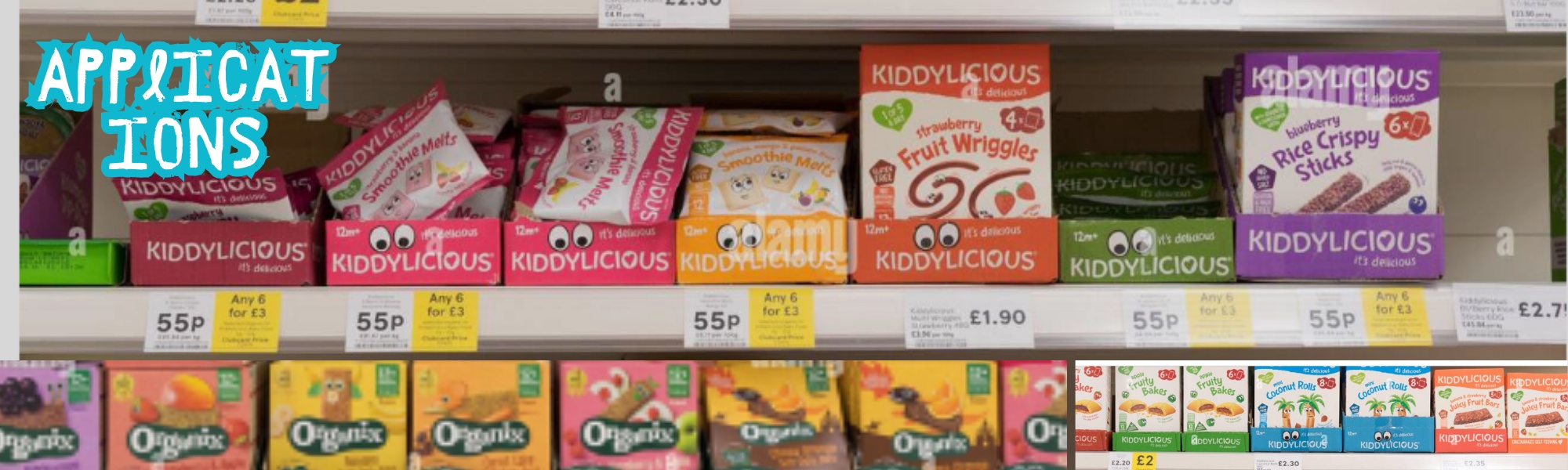
What Are The Best Materials for Making Perforated Display Boxes
The best materials for making perforated display boxes are primarily focused on durability, ease of customization, and cost-effectiveness. Here are the top materials commonly used:
1. Cardboard
- Description: Cardboard is a widely used material for perforated display boxes due to its lightweight nature and structural integrity.
- Benefits: It is easy to print on, making it ideal for branding and product information. Cardboard can be easily die-cut to create perforations without compromising its finish, allowing for effective display and dispensing of products.
2. Corrugated Cardboard
- Description: Corrugated cardboard consists of a fluted layer sandwiched between two flat liners, providing additional strength and durability.
- Benefits: It is suitable for heavier items and offers excellent protection during shipping. Common thicknesses like E-flute and B-flute are used, depending on the required strength and product type.
3. Kraft Paper
- Description: Kraft paper is known for its strength and durability, making it a popular choice for eco-friendly packaging solutions.
- Benefits: It is biodegradable and recyclable, appealing to environmentally conscious consumers. Kraft paper can also be easily perforated and printed on, providing a rustic aesthetic that enhances product appeal.
4. Paperboard
- Description: Paperboard is a thicker type of paper that is often used for packaging and display boxes.
- Benefits: It provides a sturdy structure and a smooth surface for printing, making it suitable for high-quality graphics and branding. Paperboard is also easy to perforate, allowing for creative designs.
5. Eco-Friendly Materials
- Description: Many manufacturers are now using eco-friendly materials that are biodegradable or made from recycled content.
- Benefits: These materials align with sustainability goals and appeal to consumers looking for environmentally responsible packaging options. They can be used in conjunction with traditional materials to create a more sustainable product.
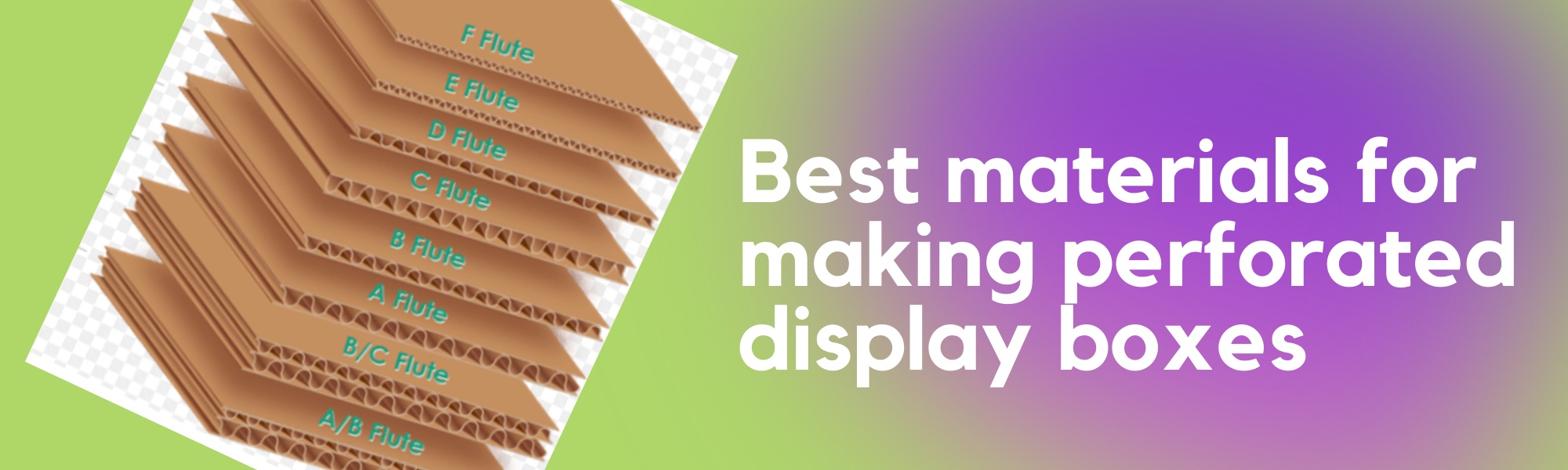
The perforation process can significantly impact the durability and structural integrity of corrugated boxes. Here are the key ways perforations affect box strength:
Reduction in Compressive Strength
- Perforations act as weak points that reduce the overall compressive strength of the box.
- The position of the perforation is crucial, with perforations at 0° angle (parallel to the machine direction) having the greatest negative impact on compressive strength.
- As the angle of the perforation increases, the reduction in compressive strength decreases.
Loss of Bending Stiffness
- Bending stiffness, which contributes to the box's rigidity and protective capabilities, is reduced by the presence of perforations.
- The angle of the perforation position has the greatest effect on bending stiffness, with perforations at 90° (perpendicular to the machine direction) causing the largest decrease.
- Using angled perforations below 45° or minimizing perforations in the cross-direction can help maintain bending stiffness.
Factors Affecting Durability
- The type of perforation (ratio of cut to uncut material) has a quantitative but not qualitative interaction with the box's durability.
- The quality (thickness and construction) of the corrugated board used in the box also influences how perforations impact durability.
Mitigating Durability Loss
- Using thicker, higher-quality corrugated board can help offset some of the durability losses caused by perforations.
- Careful perforation design, such as minimizing the number of perforations, using angled perforations below 45°, and optimizing the perforation pattern, can help maintain the box's structural integrity.
In summary, while perforations are necessary for creating easy-open and shelf-ready packaging, they do compromise the box's durability to some extent. Manufacturers must balance the need for perforations with the requirement for sufficient strength to withstand shipping and handling stresses.
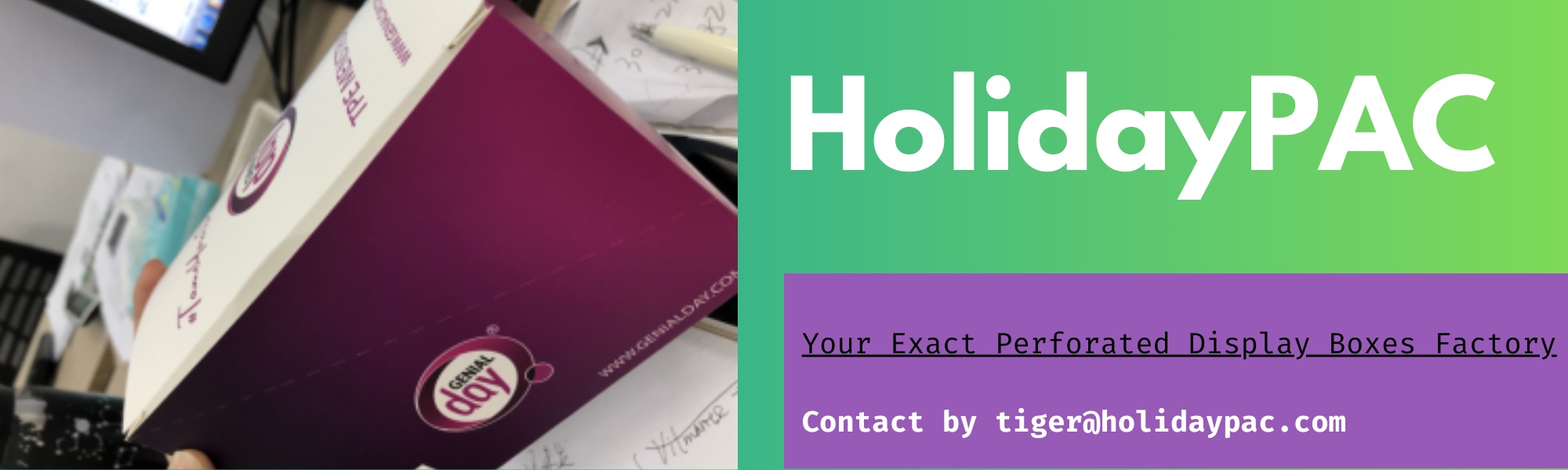